Have met some stubborn engineers which only prefer 14in popular size decanter centrifuges, and never mind the qty it will be used, also some others who only prefer the big bowl one, and no matter how big it is. Before it was a problem, back to the time GN only offer 14in and 18in, as it was popular. Nowadays, since we have upgraded our manufacturing system, and also keep learning and optimizing our managing system. We are now able to supply not only 22in, also 30in centrifuges, while the inside screw size is bigger than 14in, neverthless the length / diameter ratio, most of them can upto 1:4 now.
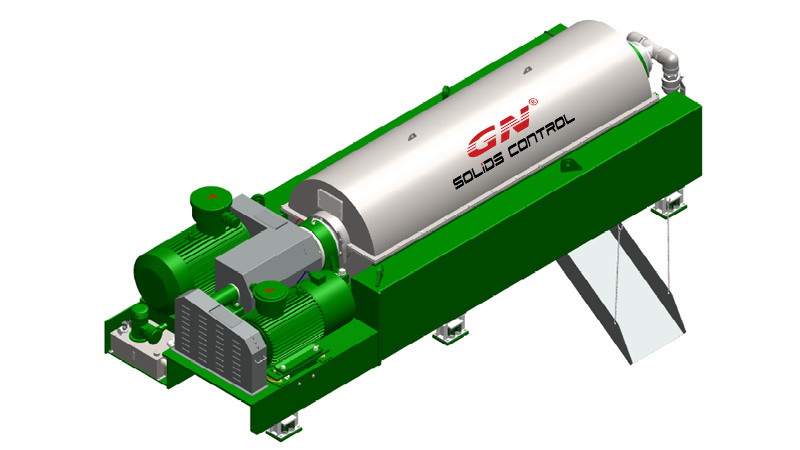
The GN 30 inch (760mm) bowl diameter decanter centrifuge is a big bowl centrifuge. GN 30inch centrifuge is with bowl length and diameter ration of 4.2:1. This bowl size allows client to handle big volume fluids with one single unit. Because of GN unique design for the screw and bowl, the GN 30 inch decanter centrifuge is design for best performance in Tunnel Boring Project Mud Cleaning, Dredging Slurry Separation, and Municipal Sewage Sludge in Purification Plants, Industry Waste Water Treatment.
According some feedback regarding GNLW553, we have upgrade the new generation to GNLW554, to make sure it have higher flow rate, and better fluid / solid result. With the modenized machine, it is not so obvious increasing the cost. This Fully Variable Speed VFD controlled unit is built using the most reliable and robust electrical components, with either ABB or SIEMENS brand variable frequency drive units. Electronic load sensing and feed pump control permit automatic optimization of the feed rate, bowl speed, and differential conveyor speed.
This may not be related to this title, but the GN 9in baby centrfuge is also have higher ratio.
Keep tune on GN big bowl centrifuge, if need more information, pls let us know.